本文详细列举了零件设计过程中常见的多种失误情况,包括通孔与螺纹孔不匹配、未设计工艺圆角及沟槽、未考虑装配便利性、未考虑常规加工手段、未考虑焊接变形等问题,并结合实际例子和图片进行说明,为零件设计新人提供参考,帮助其避免在设计中出现类似错误。
在零件设计领域,存在着诸多容易被忽视的细节问题,这些问题若处理不当,极有可能导致设计的零件无法正常使用甚至报废。以下为大家详细介绍一些常见的设计失误情况。### 通孔和螺纹孔不匹配问题在设计相互连接的零件时,可能会出现通孔和螺纹孔不匹配的情况。例如,某些零件装配时,就需要进行二次加工扩通孔处理。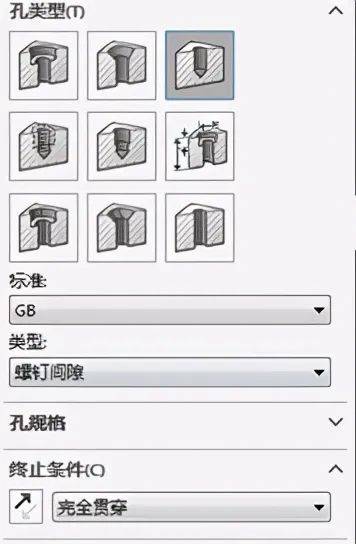这里要注意,像标注为M14的普通粗牙螺纹,其螺距为2 。如果在装配时螺纹与外购件不匹配,就像此案例一样,最终会导致设计的连接件报废。### 缺乏工艺圆角及工艺沟槽设计出的零件没有工艺圆角及工艺沟槽,会使普通加工手段无法完成加工。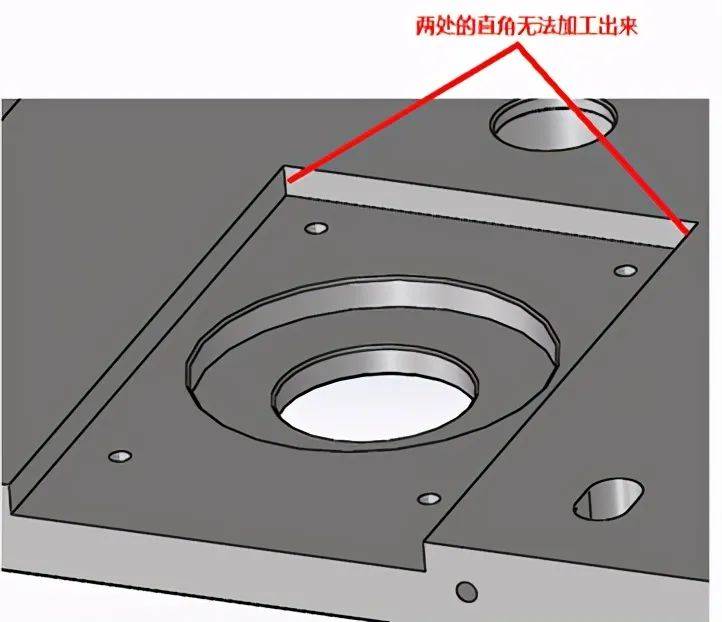当设计的零部件中涉及轴放进孔里的情况,如轴承与轴承座的安装、轴与轴承内孔的安装等。除过盈配合和部分过渡配合外(相对较少用到),都需要考虑公差配合。原则是轴的直径上偏差不得大于孔的直径下偏差,否则轴将装不进孔里。公差配合的选择可优先参考下图(机械设计手册《精度设计》及中望CAD和Solidworks里都有)。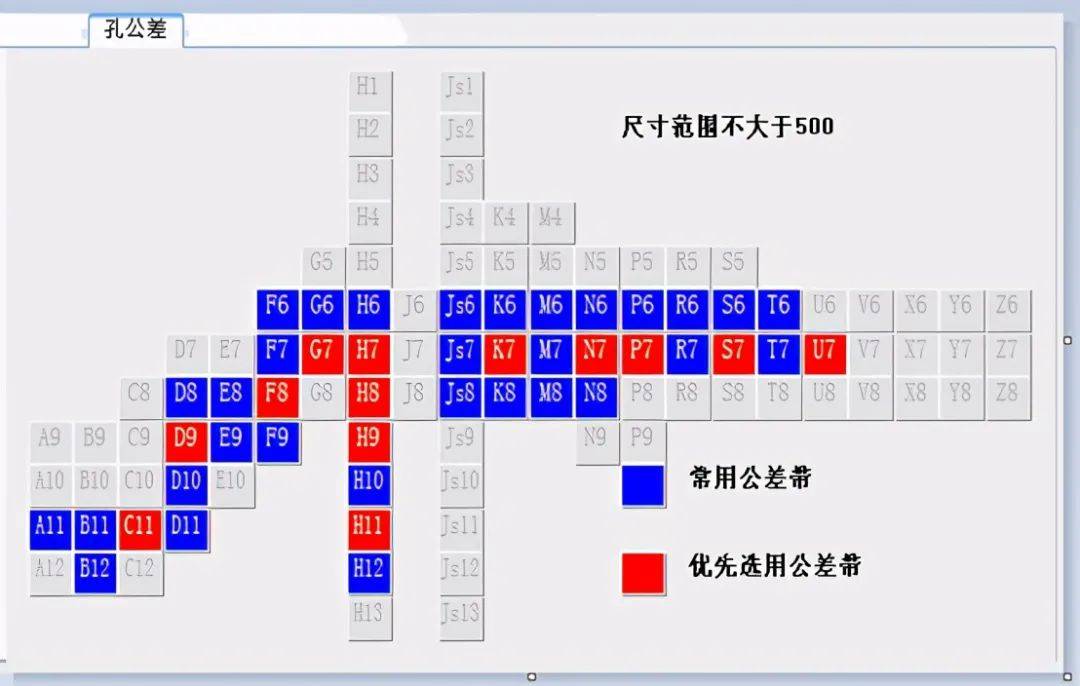同时,在设计零件时,装配的便利性也至关重要。比如无定位之口的设计,在焊接拼装时很容易将法兰和钢管焊偏(不同心),从而引发新的问题。而有定位止口的设计,焊接操作人员只需将钢管放置进止口便可轻松准确定位进行焊接。所以,设计定位止口是非常必要的。### 未考虑常规加工手段设计零件时若没有考虑常规手段能否加工,也会出现问题。以设计一个焊接件为例,最终加工完高度要求100mm 。如果按照左图设计,拼接完焊接前总高度就到100mm了,但由于焊接变形和焊接收缩,焊接完成总高度会小于100mm 。当加工上下两个法兰面到需要的平面要求时,最终其总长度就会与原设计要求相差很远。而右图在设计零件图时考虑了加工余量,零件拼接完后总高度为104mm ,上下两个法兰面各有2mm加工余量,足够加工到目标尺寸。新人在设计此类焊接件时往往容易忽略放加工余量,最终基本都会导致零件报废。### 未考虑焊接变形及拼装误差设计焊接件时没有考虑焊接变形,及焊接拼装误差,会出现焊接件安装孔在零件上打好再焊接后,孔的位置不对,导致无法安装的情况。### 材料选择不当对于需要使用线切割或者电火花等特种加工才可以完成的零件,若材料选择了非金属(如尼龙1010),就会出现问题。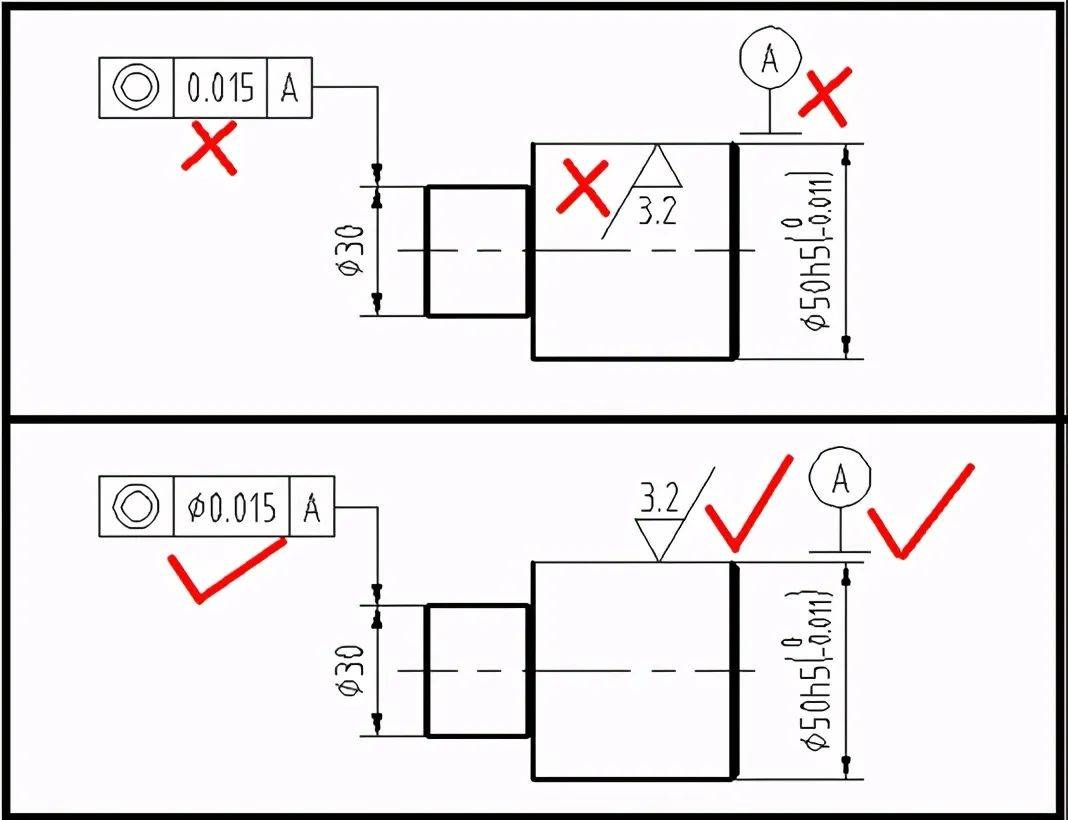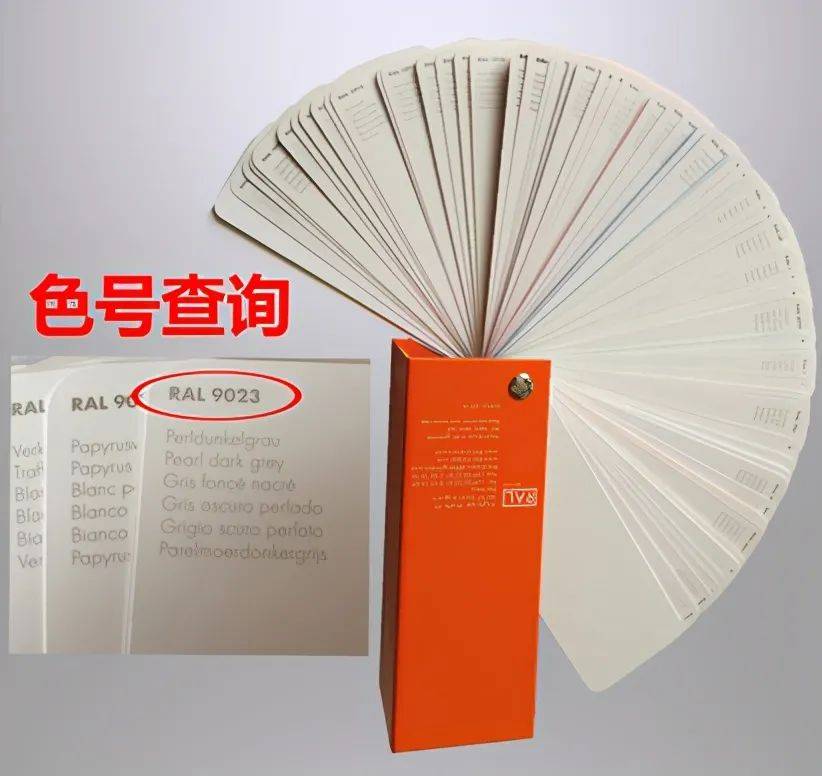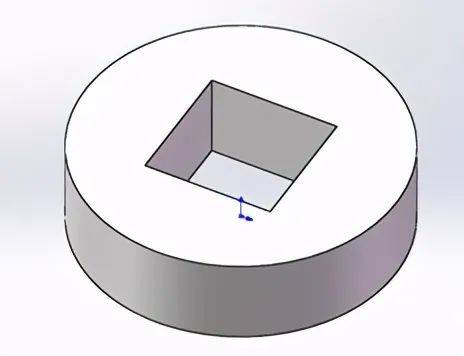非金属材料绝大多数都是绝缘的,尼龙1010也是如此,其绝缘特性决定了不可用线切割或者电火花加工。选用非金属一般考虑减震、润滑等特性,对于这种特殊形状及加工难度的零件,材料可尝试选择黄铜H62,其特性相对接近。### 尺寸基准选择问题设计零件时,尺寸基准选择不当也会影响装配。若两个零件所标尺寸基准选择不合理,可能会由于外形尺寸的自由公差偏差导致孔位整体偏差,最终导致两个零件无法装配。所以,标尺寸时应充分考虑所标尺寸的基准选择,减少累计误差导致的最终装配问题。### 未考虑工艺沟新人在设计零件时通常不会画出退刀槽,由于对退刀槽的认识不够便容易忽略,其实它非常重要。如内外螺纹如果螺纹根部没有设计退刀槽,那么与其配合的螺纹连接件无法拧到与螺纹根部的端面接触,通常容易造成所设计的零件不可用。还有就是在加工高精度安装面及阶梯轴时在轴肩根部需要设计退槽,这样可以使加工道具加工到整个圆柱面。希望广大零件设计新人能够从这些常见错误中吸取教训,在设计过程中更加严谨细致,避免不必要的失误。
本文全面阐述了零件设计过程中常见的多种失误,涵盖了通孔与螺纹孔匹配、工艺设计、加工手段、焊接变形、材料选择、尺寸基准以及工艺沟等多个方面的问题,并结合实际例子和图片进行详细说明。通过对这些问题的分析,旨在帮助零件设计新人认识到设计中的关键要点,提高设计质量,避免因疏忽导致零件报废或无法正常装配等问题。
原创文章,作者:Edward,如若转载,请注明出处:https://www.yanghehb.com/4807.html